(주)케이펙한국산업 교육센터 대표
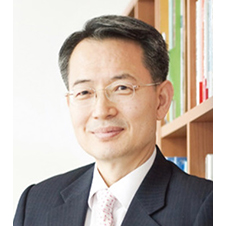
[ 충청매일 ] 도요타생산방식의 창시자인 오노다이이치의 수제자로 알려진 혁신의 대가 일본의 야마다히토시 PEC소장은 "도요타가 오늘날과 같이 꾸준하게 이익을 내는 기반에는 위기의식공유"라고 했다. 혁신의 본질은 지금의 방식으로는 생존이 안 된다고 하는 위기감속에 매일같이 자신이 소속한 현장을 개선하는데 있다는 것이다. 혁신의 목표중 하나인 이익을 높이는 것은 크게 보면 고객만족에 있지만 이를 달성하는 방법은 제품을 만들고 운반하는 전 과정에 소속한 모두가 위기의식을 갖고 개선하는데 있다. 개선의 목표는 명확하다. 고객의 가치를 낮추는 개선이 아니라 제품을 만드는 과정속의 낭비제거를 통한 원가절감과 과정마다 완전한 품질은 만드는 불량제로 활동이다. 도요타는 이를 인변붙은 자동화의 철학과 시스템으로 달성하고 있다. 이는 불량을 만들지도 않고 후공정으로 보내지도 않는다는 개선실천방법론이다. 따라서 그들은 만드는 과정에 철저하게 불량방지 시스템을 만들어서 불량이 날 가능성이 있으면 센서가 감지해 기계가 멈추도록 한다.
또한 사람이 생산하는 공정에서도 조그마한 이상이라도 감지하면 작업자가 우선 라인을 세운다. 우리는 금기시 하는 것이 라인 스톱이지만 도요타의 현장은 작업자가 할 수 있는 아주 자연스러운 것이다. 자주 세운 곳은 집중 개선의 공정으로 지정하고 개선을 통해 매일같이 생산성이 오르는 효과를 낸다. 라인을 세워서 문제가 되는 것이 아니라 문제로 인해 위기감을 느껴 신속한 근본개선이 가능해진다는 것. 또한 불량이 만들어지지 않고 뒤 공정으로 불량이 흘러가지 않게 되는 것이다. 이러한 사고방식을 바탕으로 그들은 매년 90만건이 넘는 카이젠 제안과 개선으로 낭비요소를 철저하게 제거하고 있다. 그들의 제안은 위기감의 산물이었다.
이의 효과는 도요타를 비롯해 협력기업에서 그토록 많이 존재해야 할 검사공정이 없어진다. 부품공장의 출하검사는 물론 완성차 업체의 부품수입검사가 없다. 이를 바탕으로 부품재고의 최소유지가 가능하고 간판이라는 도구를 사용해 작업자에 의한 자동구매를 해 발주를 하는 구매 부서를 없앴다. 그리고 재고 관리를 해야하는 자재창고라는 중간 과정도 제거 했다. 얼마나 대단한 낭비제거인가? 이 과정에서 조금도 고객의 가치를 훼손하지 않았다는 사실이다. 공정이 단순화되면서 불량의 발생 요소를 없애고 획기적으로 원가를 줄여 이익이 높아지는 것은 당연하다. 또한 협력기업의 이익을 더 확보해줄 수 있는 여유도 생긴다.
그래서인지 필자가 자주 다니면서 만나는 도요타의 협력기업의 대표들과 관리자는 도요타의 정책에 대해 칭찬이 많다. 거래하는 것이 자랑스럽고 적절한 이익을 잘 확보해 준다는 것이다. 그들은 도요타의 협력사에 근무를 하면서 도요타에 근무하는 사람들을 그리 부러워하지 않는다. 도요타의 근무자들은 높은 연봉을 받을 만큼 정말 열심히 일을 한다고 협력기업의 사원들도 인정을 해주는 부분은 놀랍다. 결국 도요타는 공정속에도 고객의 변화에 민감한 조직을 만들어 위기감을 공유한다. 이를 통해 전부문의 구성원이 고객이라는 변화에 대응하는 일체감이 조성되는 조직이 됐다. 고객이 없어도 계획적으로 생산을 하게 되면 조직은 고객과 무관하게 되고 결국은 고객의 변화에 무감각한 조직으로 변질이 되는 것이다. 고객의 변화에 민감할 때 위기감의 공유가 가능해짐을 도요타의 사례에서 알 수 있다. 고객에게서 멀어지면 기업의 모든 풍요로움과 직장의 실체는 안개처럼 사라질 수 있다.